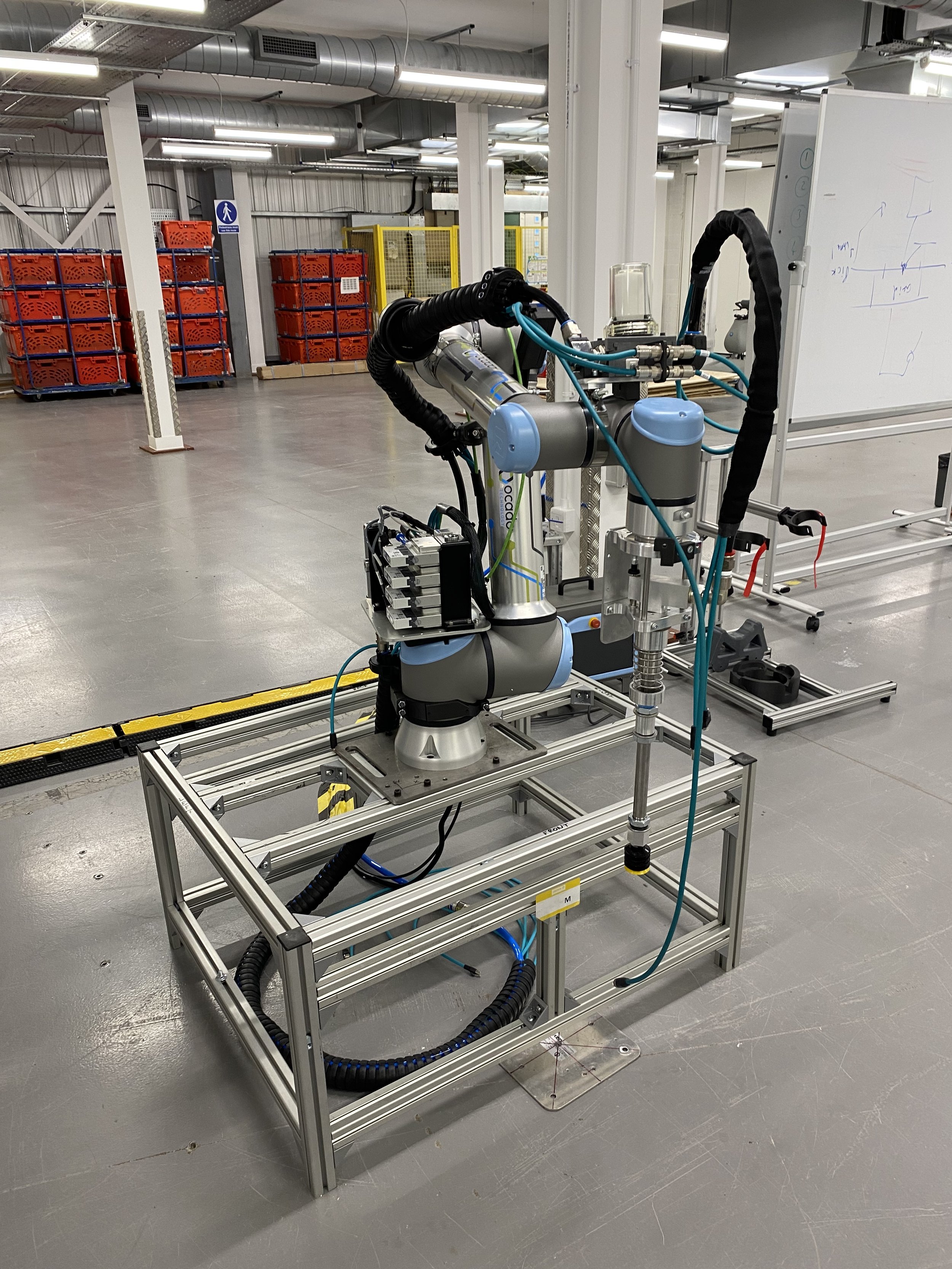
Robotic Repairs Simulation
TL:DR
Ocado had finished its DVT-1 designs for a robotic handling solution. I proposed we should test its repairability and expected maintenance approach with support engineer users before committing the final design freeze. I held a day long workshop in our lab and discovered a multitude of design issues that would make maintenance hard, as well as prompting a fundamental re-think on the support approach.
We were able to make design changes that lowered the cost of parts repair per unit, lowered the necessary repair downtime per unit and removed extraneous components lowering the overall CAPEX of the product per unit. We were also able to build a repair manual.
How did we approach it?
I ran a day-long simulated repair workshop with 3 repair engineers who had never seen the product before (but would be the repair users when the product was live), the senior hardware designer, the PM and the head of the repair engineers team who produces repair documentation.
I took each sub-system of the arm in turn and asked the users to imagine there had been a fault detected with it. The users then had to describe how they expected to diagnose the precise issue with the component and then they physically worked with the arm to remove and walk through the repair process. Once ‘repaired’, I asked the users to discuss how they would validate the fix had been successful
In this way we systematically worked our way through each part of the arm understanding what level of diagnosis was required, documenting the repair flow and determining a validation for repairs
What did we learn and Impact?
The users identified that a component swap rather than full robot change (a fundamental shift in the proposed repair approach) would be a more efficient way of working, but necessitated a stronger diagnostics system and fault tree than we had developed.
The PM shifted the software team’s focus onto the diagnostics app to facilitate this.The users identified most components that needed replacing could be better attached with click and lock mechanisms rather than screws, allowing for easy removal in difficult work environments.
These changes were made and will have significantly reduced repair time per unit, lowered overall downtime.There were aesthetic choices made for the arm that users identified would be removed on the initial repair and never replaced as they were non-functional.
We removed these aesthetic components, with an estimated cost saving of £150 per unit and roughly £9000 per site these were to be installed at.
What were we trying to understand?
How easy was the DVT-1 design of our on-grid robotic picking arm to repair?
What were the expected tools needed for repair?
What were the proposed repair solutions for each sub-component?
Where could improvements be made to improve the efficiency of repair?